CHAMPION
BLADE TECHNICIAN
For those who are happy at heights and like the idea of a job that can take you around the world, blade technicians get a truly unique view of the energy transition.
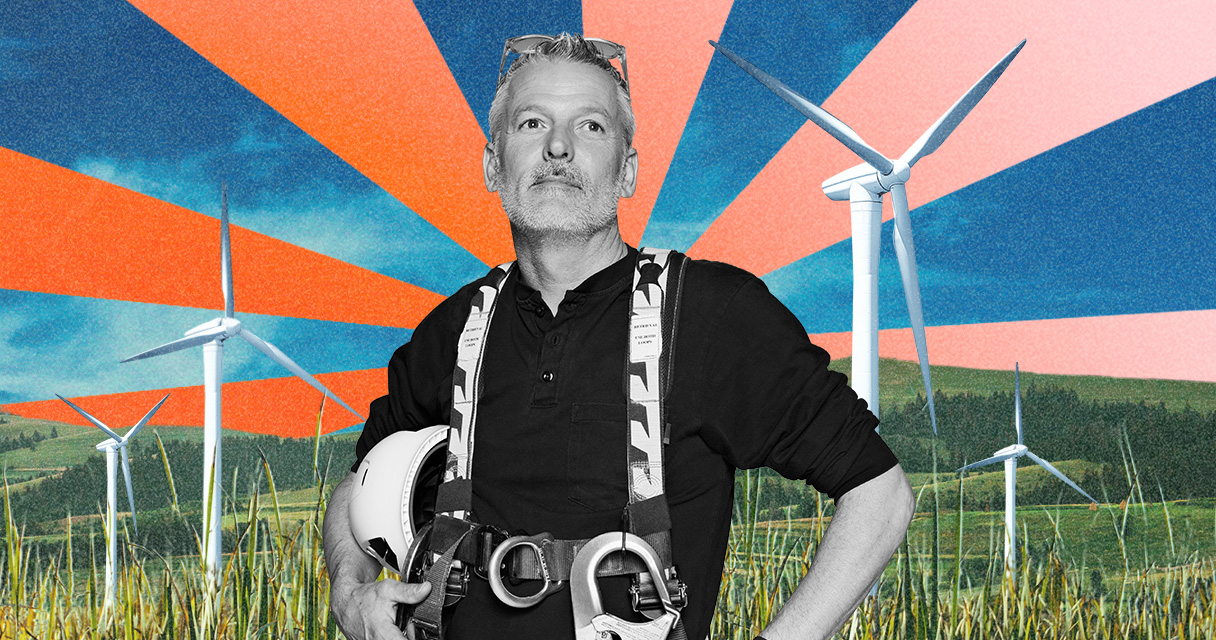
“I’ve worked on every major continent apart from South America. I’ve been from the Isle of Wight to Nebraska, and spent a year in the Baltic Sea, 49 nautical miles out between Denmark, Germany and Sweden. It’s been an interesting 20 years.”
“I love what I do, and you’ll get a job anywhere with these skills.”
When Darren Smith says “anywhere” – he’s not kidding. Having made and repaired wind turbine blades for the past two decades, Darren is a renewable energy veteran, someone with huge experience in and around wind energy across the globe.
But he didn’t begin his career in engineering. The way he tells it, the most relevant experience he had was a lifelong enthusiasm for Lego.
“I was in retail business management in the mid-2000s, and moved to the Canary Islands,” Darren says. I was working in Gran Canaria where they had these massive wind turbines, and I just thought they were really impressive.”
“When I moved back to the UK, I discovered there was a production unit on the Isle of Wight that built the turbine blades, and I applied for a job in the facility building them. I was fed up with sitting in the chair and being a keyboard warrior, and I wanted something different.”
When asked what qualifications he had for the role, Darren smiles. “I liked playing Lego. That’s my engineering background.”
“When I applied, they wanted people with no prior knowledge in the industry so they could train us to their standards. So, I came with no prior knowledge, but also no bad habits – I was a clean slate they could train exactly as they required.”
He joined a factory with 500 staff, constructing 40 metre-long blades and learning all aspects of manufacture and repair.
Two decades later, and Darren is building teams and doing that training himself.
“My title is ‘Blade Supervisor’, which doesn’t reflect exactly what I do – it’s more operations management. We’ve got a team of 20 technicians, and my role now is everything from setting up the technicians, allocating equipment, organising repair for lightning and transport damage, construction, training, health and safety on elevated work platforms…”
For people interested in working on turbine blade construction, there’s still plenty of opportunities to get into the industry, no matter your experience.
“We’re really focussed on building the knowledge and workforce here in Australia,” Darren says. “We’ve got plenty of skills we can transfer to new technicians, with a lot of experienced techs we can pair new recruits up with, and we’re building our way toward a much younger, Australian crew.”
In terms of the day-to-day work, Darren says a lot depends on which access method you’ll be using, and whereabouts on the blade you’re going to be.
“You’ll either be hanging from the outside on a rope, inside a blade, or you could be on a new build construction site overseeing inbound deliveries and just touching up transport damage.”
“The longest blades we’re putting up are 80 metres long,” he explains. “The ‘root end’ is 3-4 metres in diameter, so there’s room to move, even though you wouldn’t say they’re designed for human occupancy! There’s one particular blade that’s used offshore that you can park a double decker bus inside of the root end. These things are huge.”
Blade technicians are taught how to read schematics and data sheets, and get an understanding of chemicals used in fibreglass construction. And of course, there’s the safe work practices.
“Blade techs are the high-risk team, so health and safety is paramount.
“If you’re trained up and part of a rope access crew, your day will start with your health and safety checks. You get to the turbine, get a tag-out technician to lock it for you both electrically and mechanically so it’s impossible to move, you’ll go out and go up in an elevator, or if it’s an old turbine, you’ll climb.”
“There have been some hairy moments,” Darren acknowledges. “Sometimes it’s been human error or lack of training and knowledge, but I’ve never had a moment in my career that I’ve felt it’s time to give up. It’s just been an adrenaline rush.”
And of course, the blades are also fascinatingly complex. “They are massively complex in terms of fibreglass layup. When you get a build document from a factory, there’s a page for every layer of the fibreglass. So when you need to do a repair, you need to count through the layers to find the damage. Chances are, it’ll be page 30,” he smiles. “They now have 50-100 layers of fibreglass in different areas to enable the blades to flex and harness the wind.”
And in terms of the prior skills and knowledge, Darren says that anyone who is interested and committed is welcome to apply. “You have to be comfortable with heights and confined space, but I came from retail management and now manage blade technicians across the whole country.”
“You can come from anywhere.”
Darren Smith is a Blade Supervisor at Vestas. He gained his knowledge and skills through on-the-job training.